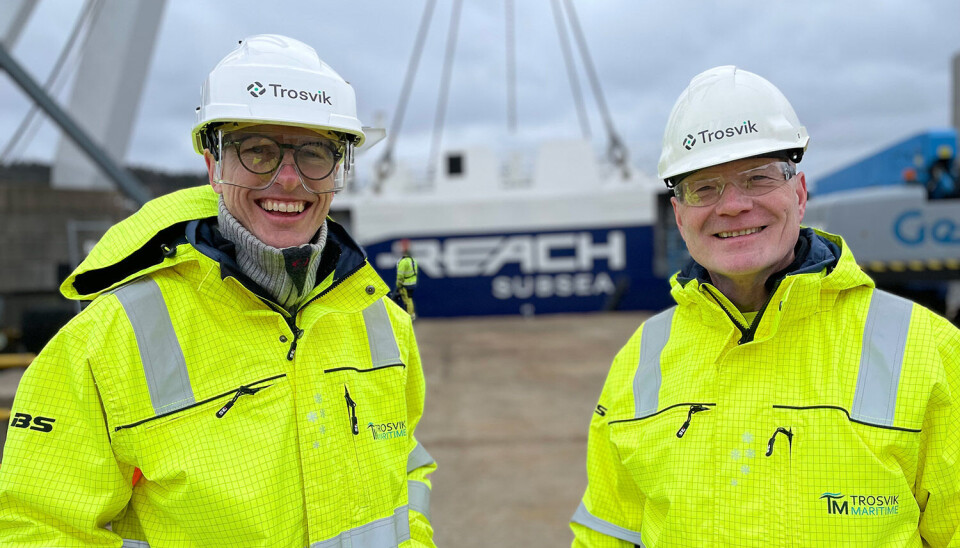
Hit the bullseye on their first try
There has been a shipyard in the Brevik area for well over 100 years. Since 2020, it has been Trosvik Maritime that has filled the workshop halls. Now they are proud to have built Ship of The Year 2024
In the autumn of 2019, the news came that the Vard Group had decided to close its operations in Brevik, in Telemark. Large financial losses, and an offshore industry that had come to a complete standstill meant that the group finally had to make the difficult decision.
Trosvik Maritime rose from the ashes in early 2020. Local investors believed that it had to be possible to operate a maritime industry in the area.
“Geir Sæther and I, who were the main initiators, thought that it must be possible to achieve something in the maritime sector. At the same time, we realised that we had to have more legs to stand on,” says Jan Brønsten, general manager of Trosvik Maritime.
The area had docks, cranes, and halls. Good relations on the supplier and shipping side were also instrumental in wanting to invest together with investors. Lots of property both in Heistad and in Brevik was bought.
“It was probably also an inherent madness that made us go for it,” says Brønsten with a smile.
“We wanted to pass on the maritime expertise and tradition that has existed in the bay, and hold on to it a bit. And then one might be a bit crazy to start up a shipyard in 2020, but recruiting from an area here in Eastern Norway within the maritime sector is also an opportunity. It is a strength that will be instrumental for us going forward,” adds Sæther.
They started quietly with service, maintenance, and rebuilding of ships at the quay, together with assignments for the industry in the Grenland district of Telemark, and some engineering assignments. In 2020 and 2021, they also had a number of ships in lay up, while the offshore segment was still struggling.
Good relationships were important
The Grenland area has around 3,000 annual calls, and they would probably like to see more service assignments go to them. But with the lack of a dry dock, it is, among other things, not possible to carry out five-year certifications.
“So, we have to compete on slightly different terms. It depends on availability, flexibility, capacity, and knowledge. It takes a little more time,” says Brønsten.
“We will focus on a combination of maintenance, conversions and new construction in the future within the maritime sector,” adds Sæther.
The project with ‘Reach Remote’ started in 2019. Two years later, in 2021, Trosvik Maritime was connected as a shipyard. From their time as part of Vard, they had already built up good relations with Kongsberg.
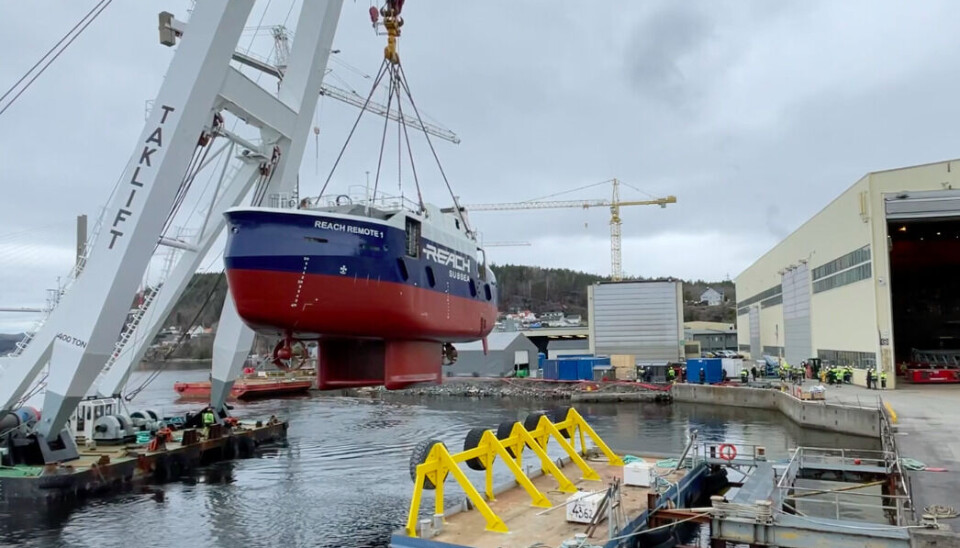
“We knew them very well for many years and have built many (of Kongsberg’s) UT-designs here. So that's how the contact came about. And then it is part of the story that we, as a newly started company, put the lion's share of our investments into buying property. That meant a less robust economy, and limited opportunity to run normal ship contracts with full guarantees. We have to build stone by stone and seek value chains where there is a slightly different setting. Where perhaps the shipowner, and in our case with Kongsberg, may be able to relieve the burden with liquidity. We achieved that in this consortium,” explains Brønsten.
There was thus a lower financial risk for the relatively new company to participate in the project.
Differs from normal contracting for new construction
Reach Subsea has a contract with Kongsberg, which delivers a finished product, and Kongsberg in turn has a contract with Trosvik Maritime.
“We are a subcontractor, where Kongsberg has design, engineering, automation and product responsibility. In this case, they have an extended responsibility where they actually deliver the vessel to Reach as a turn-key project,” says Brønsten.
Since this is a completely new way of contracting/building a vessel, some interfaces have appeared that had not been anticipated. Simply because it has not been done before.
“But we have solved it. Kongsberg is more used to being a design and equipment supplier, we are used to being a shipyard and together we have solved the challenges that have arisen amicably throughout. There is more learning, and great opportunities, by looking at the value chain going forward with Reach, Kongsberg and Trosvik. We hope to help build on this,” says Brønsten.
Both vessels for which they have a contract are floating on the water now, with the first going to SAT (sea acceptance trials) in the transition August/September and HAT (harbour acceptance trials) starting on number two with delivery in Q4.
Troubling times
The hulls of the two vessels were built at the Passer shipyard in Klaipeda, Lithuania. It was a new acquaintance for Trosvik Maritime, where the head office of Passer Group is located in Sandefjord. But the shipyard faced challenges with manpower as Ukrainian workers wanted to return home to fight for their country. In addition, steel prices rose significantly.
“It was very challenging. But what they delivered in the end, with quality and scope, was very good. Deploying hulls with regard to the aforementioned challenges, such as war and steel prices, was no less demanding because the ship contracts are development projects. It took longer than we had planned, but the quality and the final result were good,” says Sæther
The fact that the vessel is small does not mean that it is necessarily easier to build. Quite the contrary. ‘Reach Remote 1’ is more technically complex than a medium-sized platform supply vessel, at only 24 metres. If you include an ROV, it is very tightly packed.
“It has been exciting, and it is incredibly educational, although it is very demanding from time to time with space on board,” says Brønsten.
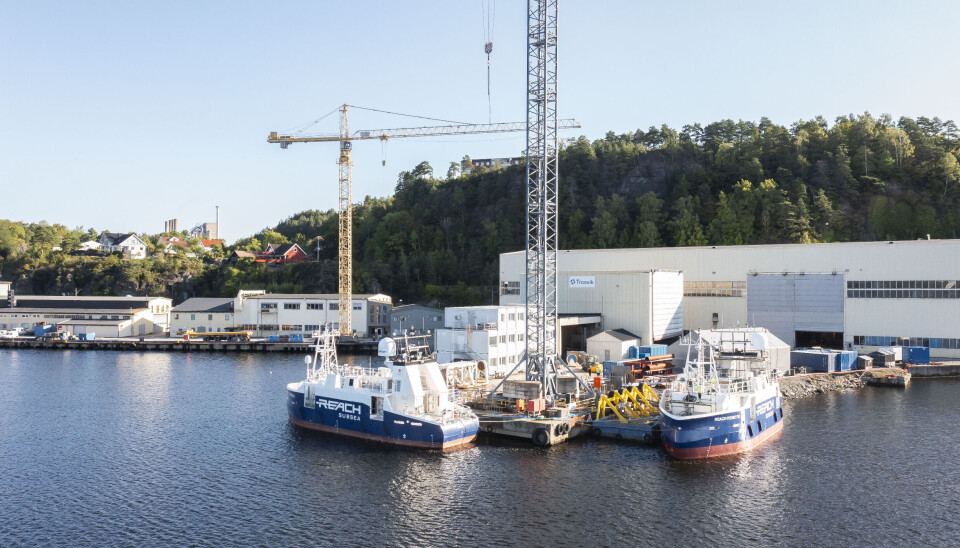
Because where one has quite a lot of space on a normal ship, it is more complicated on a small vessel like this. Everything must be planned and done in the right order to reach the goal.
“As many standard components and equipment as possible have been chosen for the project. This equipment is put together in a way and with functionality that has not been done before. This can now be seen in the commissioning and test phase. A number of challenges arise along the way that must be resolved together with the supplier of the components, since it is only now that the functional test together with the associated equipment is carried out on board. It is very demanding and requires a slightly different way of thinking and expertise,” says Sæther.
But all that they have learned from orders and sequences on vessel number one, they have taken with them into the construction of number two. The changes that have been picked up there, means that it has been much easier the second time around.
“For the next builds, it will be even easier based on systematic learning and focus from partners. Where the product will also appear to be of the highest quality,” says Brønsten.
Great fun to win
“What did you think when you found out you had won?”
“It is incredibly rewarding and exciting, and gives us a lot of energy. Then you get a lot of pay for your hard work. There is a pat on the back for all employees, especially those with innovative thinking and new technology. Even though we have worked with boats and maritime for a long time, it is great fun to win with Trosvik,” says Brønsten.
“Branding and announcing that Trosvik deals with service, maintenance, and new construction. It is an excellent opportunity for us through this Ship of The Year award,” says Sæthe.
He adds: “We had a visit from one of Reach's customers recently and he had been given a tour of the shipyard and been on board the boat and when the whole session was finished he just said... This is the future Geir. So, he was completely convinced that this was the right concept for the tasks they will be solving in the future.”
“We are very proud and happy that both Reach and Kongsberg wanted to bet on us, which is a big feather in the cap for the entire maritime environment in Trosvik,” concludes Brønsten.