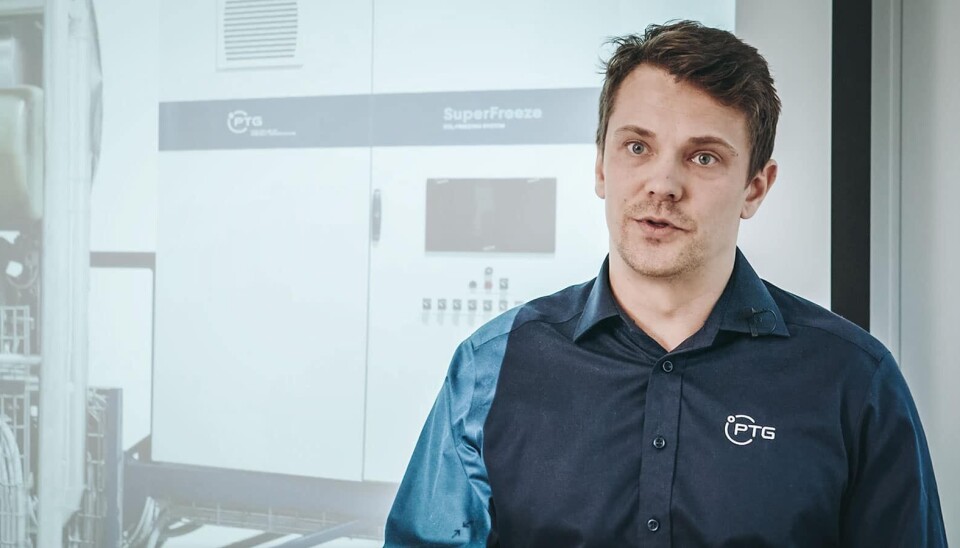
Contributes to better quality and reduced wastage
PTG will deliver cooling and freezing solutions to Bluewild's "Ecofive". “Our solutions must contribute to better quality and reduced wastage throughout the entire cold chain. When using natural refrigerants and reduced energy consumption, our systems also contribute to a better climate and increased profitability,” says Roy Arild Fjellstad, sales manager for marine and industry at PTG.
PTG develops and supplies environmentally friendly cooling, freezing and energy-efficient solutions, and is a significant supplier to both the grocery industry in Norway and the seafood market both nationally and internationally.
“We know that the value of the final product increases when the fish is chilled and frozen while it is at its freshest, and while the nutrients are at their peak. Our solutions also ensure improved operating economy through reduced fuel consumption and fewer operating hours,” says Roy Arild Fjellstad, sales manager for marine and industry at PTG.
PTG works together with customers to find the perfect temperature and solutions that are cost-effective and environmentally friendly. The name PTG is taken from the initials of the holding company Perfect Temperature Group - and the slogan of the group; the value of perfect temperature. PTG is the result of integration between the companies Kuldeteknisk, FriNordica, Kjøleservice Helgeland and Multi Kulde in Bodø.
“Our solutions must contribute to better quality and reduced wastage throughout the entire cold chain. By using natural refrigerants and reduced energy consumption, our systems also contribute to a better climate and increased profitability,” says Fjellstad.
Focuses heavily on fish welfare and quality
With "Ecofive", Bluewild has invested heavily in good fish welfare and a high quality standard for the raw material. The refrigeration and freezing solutions on board are central to the value chain.
PTG collaborates with several of the other suppliers, and must, among other things, ensure perfect temperatures with the least possible energy consumption for the refrigerated seawater (RSW) plant, the plate freezers, the IQF (Individually Quick Frozen) freezers and the freezer storage on board.
The freezer capacity is 65 tonnes per day, divided into 25 tonnes in the IQF freezers, and 40 tonnes in the plate freezers.
“We make sure to take care of the good quality of the fish by starting the cooling process as soon as the fish has been bled. The SeaCO₂ol RSW plant cools the seawater in the cooling pipes, and also delivers chilled seawater to the factory to prevent the fish from heating up during the process,” explains Fjellstad.
The fish are taken alive from the trawl through a pipe system below the waterline to water-filled receiving tanks. There, the fish are recovered and kept alive before being electrocuted and bludgeoned. The fish are then taken further through cooling pipes which give the fish a lower temperature, and thus contribute to faster freezing.
Each fillet is quickly frozen - and the remaining raw material is preserved
The fish is kept chilled throughout the process, and is quickly frozen to minus 35 degrees with the SuperFreez freezing system after it has been processed in the factory on board.
IQF freezers ensure that each fillet is quickly frozen. The residual raw material must also be preserved in the best possible way, and frozen in plate freezers with automatic bottom emptying.
“With rapid freezing, and freezer storage with cold temperatures, Bluewild will be able to preserve the fresh and good quality of the fish from the time it is brought on board until it is on the plate for the consumer,” says Fjellstad.
When the fish is frozen quickly, fewer ice crystals form than when it is frozen slowly. Larger ice crystals damage cells and tissue fibres. Therefore, rapid freezing and low freezing temperature reduce cell bursting in the freezing process and during thawing.
Natural refrigerants
Both the SeaCO₂ol RSW system and the SuperFreeze freezer system use the natural refrigerant CO2 (carbon dioxide) .
“CO2 is a natural, robust, well-tested and environmentally friendly refrigerant both in industrial plants on land and on board fishing boats,” says Fjellstad.
“When it comes to energy optimisation, with the new system we can adapt the freezing capacity to the cooling demand at any time. Heat recovery from CO2 plants is also very beneficial. Our systems thus help to reduce the total energy and fuel consumption on board. The technology is environmentally friendly, it is energy efficient, and not least it contributes to significant quality improvements in the catch,” concludes Fjellstad.